Improve your efficiency using LEAN Tools
The LEAN methodology will get your productivity and effectiveness to the next level.
Too many companies nowadays speaking about LEAN actually speak about 5S methodology, but those are forgetting that LEAN production contains a variety of different tools and methods. For example, Andon can be a key element for your efficiency at work. The LEAN methodology can consistently improve overall company/business and individual employee productivity as well.
Our aim is to present you with the most comprehensive source of simple information to assist you in improving the productivity, efficiency, effectiveness, product quality, and profitability of your production processes.
WHAT EXACTLY IS LEAN PRODUCTION?
The underlying concept of lean production (also known as lean manufacturing) is actually fairly simple: strive diligently to eliminate counterproductive things from the manufacturing process. How to understand what are the counterproductive things in your company?
Read ahead to find out.
Toyota, Intel, and Nike are examples of well-known firms that implement LEAN. The method is based on the Toyota Production System, which is still applied by Toyota and numerous other companies. A lean manufacturing system might assist companies that employ enterprise resource planning (ERP) [1].
Lean production was brought to the Western world in 1990 based on MIT research on the future of the vehicle described by Toyota’s efficient production strategy – The Machine That Changed the World [2]. Since then, continuous improvement principles have had a major impact on manufacturing ideas worldwide. As well as industries besides production, such as healthcare, systems engineering, and service sectors.
Kaizen [3], or continuous process improvement, is one of the guiding concepts of LEAN manufacturing, which focuses, among other things, on eliminating inefficiencies [4].
But did you know that there are 8 inefficiencies in LEAN production? Shall we discuss them first and later on provide some examples for you on how to solve some of them? And indeed come back to the list to understand and see which one was given in the example.
The eight inefficiencies of lean manufacturing
The Toyota Production System identified seven wastes or procedures and resources that do not add value to the customer’s experience. These are the seven wastes:
- Transport – redundant mobility.
- Inventory – leftover goods.
- Motion – unneeded movement of people, equipment, or machinery. For example, employees go to managers when they are unavailable, get back, then go again.
- Waiting – waiting, either for people or inactive equipment.
- Overproduction – a product’s overproduction.
- Inefficient operations. Over-processing or spending more time on a product than a buyer requires, such as designs that necessitate high-tech equipment for superfluous features.
- Poor quality – and flaws that necessitate time and money to fix.
Have you ever tried to analyze your business considering these?
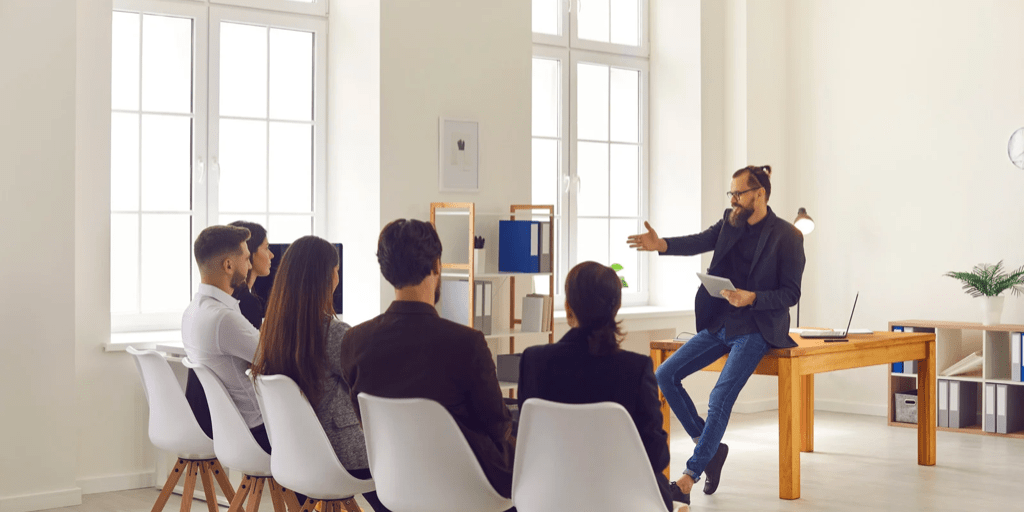
Let’s move to - how to improve your productivity by applying LEAN tools. Exact practical examples:
When you are a manager or a team leader with a bunch of responsibilities on your shoulders and your team consists of more than a couple of members. In a rapidly changing and highly stressed work environment, it could be very challenging to give all the attention to each employee when needed.
Everybody gets anxious: employees trying to get their questions answered and team leads trying to deal with randomly coming requests unproductively. They are not masters of their time anymore, some are waiting others are trying to get out of the hamster’s wheel. But what if there were a simple system how to inform a manager that an employee needs help, what exactly type of help does he/she needs? What if there is a simple system where the manager can gain her/his control of time back and plan work according to priorities?
The Good News
LEAN already has that system simple and intuitive, what’s not less important and easy to implement – it’s Andon. Andon is a visual alert from the employee to the team lead to inform them that help is needed. Whether the production process stopped, questions came, or quality issues are identified – the employee makes it visible to the manager that he/she needs attention.
Manage your priorities, inform others, and communicate using different colors, visual images, and text messages with your team and co-workers. Seamlessly switch on to your next task, and wait for the manager to come to help. Don’t waste your time trying to grab your manager’s attention. Eliminate the common inefficient practice “He who shouts the loudest gets heard”, and optimize.
Just understand that there is a difference – when you have your problems, and behind your back, there is another person with its problems – and it’s your work (as a manager) obligation to solve them. There is less pressure and more productivity when you see the light and know exactly what you need to solve due to its color. Despite Andon with its three colors – it’s possible to have other different colors. But that is going to work in cases when you’ve dedicated your time and taught workers – which busy light color means what?
From our side we can suggest the next colors and the meaning behind them:
- Green. In case everything is fine.
- Red. When there is any problem (Andon, undone?) – so, the manager can come and solve it, but you at the same time have time to do other things needed.
- Yellow. Is used when someone has any questions. OR idle time = when you can’t do anything during production time.
- Blue. When you are almost finished and you are ready to receive the next materials, resources, or task.
- Another color can be used if you still have unsolved issues and need the manager to come to you when he/she is free.
This strategy is used in plenty of top-level companies. For instance, Google as of now is using a hybrid work idea, where some workers are doing their job from their headquarters offices and some from home. While issues from home can be easily solved by software with colors, at a physical work office it’s way more effective to see something physically. And you can collide the physical world and software, so if color and light activate – it gives a notification to the software. In this case, the suggestion would be to consider – these availability indicators.
It doesn’t have to be a big busy light to understand – what is happening and what status you have as a worker. You can program any additional color with your meaning behind it. Just don’t forget to tell your colleagues about which color means what. This is a modern way of solving challenges at work, with amazing, innovative forms which give the opportunity to upgrade your company’s image.
Also, don’t forget that you can operatively solve problems with this do not disturb light as a part of the LEAN strategy.
And even in cases when what was written above is not an example that refers to you exactly – draw parallels. Meaning – try to look at your case from a prism that was given in the example and adapt it to your situation.
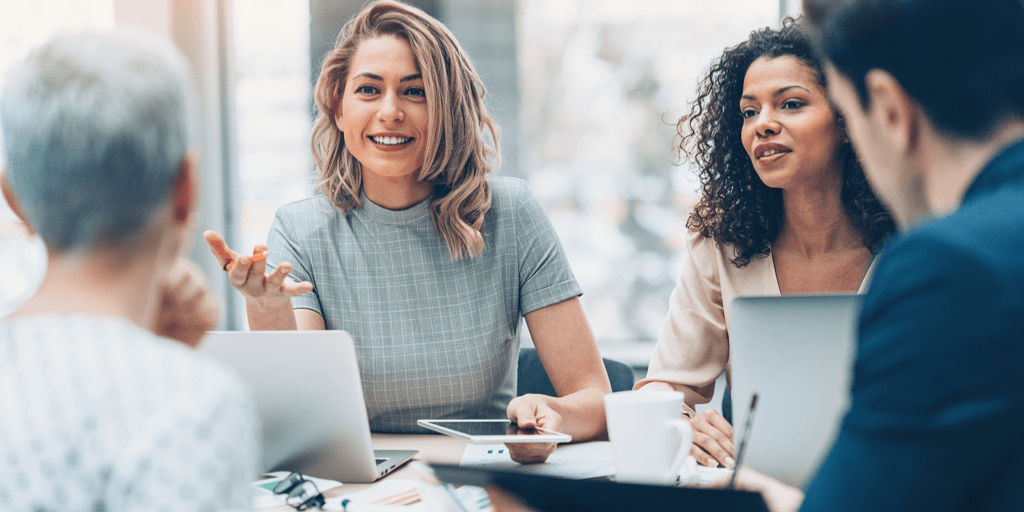
Wow! You are here, that’s amazing! If you remember there was something odd in previous sections – we have talked about 8 inefficiencies, but listed only 7, did we make the mistake?
No, no, no, don’t underestimate us. Just, due to that it was not initially incorporated into the Toyota Production System, many lean practitioners refer to a #8 waste:
8. Unrealized talents and creativeness.
And here we come to the next question:
What do you think were the inefficiencies that we’ve discussed in examples in the main text?
To finalize
Lean manufacturing is an approach for optimizing and improving production processes or other services in order to give greater advantages to consumers while minimizing costs and time via waste removal.
Lean is effectively implemented across an organization as a strategy, with continuous monitoring and changes implemented with the assistance of personnel at all levels.
Suggestions from our side – which Actions to take: 1. Be reasonable about what’s achievable. 2. Lean is dependent on people, hence educate all employees. 3. Encourage employees in the company; they are specialists. 4. Accept the concepts and philosophy of kaizen.
Actions to avoid: 1. Don’t strive to be overambitious.
LUXAFOR HELPS PEOPLE TO ACHIEVE THEIR GREATEST PRODUCTIVITY LEVELS WITH A WIDE VARIETY OF OFFICE PRODUCTS. LET’S BE PRODUCTIVE TOGETHER!